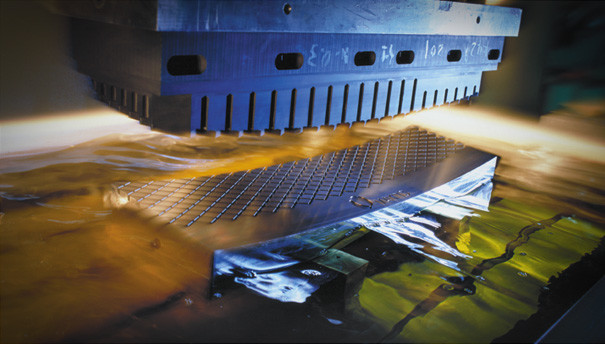
The whole method takes place during a material tub like oil or deionized water. EDM was developed throughout the Second warfare by the Lazarenko Brothers within the land and has since evolved into a significant business with many styles of machinery. Electrical spark discharges have long been a way for achieving extraordinarily high temperatures. In EDM processes, the plasma-like ten,000 C temperatures will produce a posh atmosphere at the microscopic level on the work surface.
While it\'s typically understood to be a warmth melting method, what\'s really happening on the work surface continues to be a topic of analysis. the main challenge in economical EDM process is management of conductor. There square measure different parameters, as well as conductor form for a few processes – problems that created pc numerical management a breakthrough technology for widespread adoption of EDM.
Three major styles of EDM machines
While there square measure various specialty styles of discharge machining, industrial machines square measure normally classified into 3 categories:
Wire EDM
Die sinker or ram EDM
Hole drilling or “hole popper” machines.
As the name implies, wire EDM uses a skinny wire because the conductor, that carries the spark causing electrical potential. it\'s programmed to maneuver during a fastidiously controlled pattern roughly analogous to a woodworker’s sawing machine. management of the wire movement in associate degree XY plane is analogous to different CNC-driven technologies, however with the distinctive conditions of EDM and special needs. Logical discharge erodes the conductor in addition because the work, therefore usually a spool of wire is employed for the conductor, passing unendingly by motor drive to gift a recent discharge path within the cut.
Also, throughout the method associate degree unstable discharge may be created if the material breaks down within the cut region, or wear rubbish contaminates it. management natural philosophy will compensate to a definite extent, however clean material fluid should be pumped-up frequently to flush the cutting zone.
The “cheese cutter” wire EDM technology is well-liked, however has one necessary limitation: wire should pass entirely through the work, creating basically a two-dimensional cut during a three-dimensional half. complicated cavity shapes that square measure required in several tool and die applications, like metal stamping dies and plastic injection moulds may be EDM processed mistreatment “die sinker” (sometimes known as “ram”) EDM.
In this method, associate degree electrically semiconducting atomic number 6 conductor is machined exactly to create a “positive” of the specified cavity that\'s fastidiously plunged into the work. Logical spark happens over the surface of the atomic number 6 conductor. the flexibility to provide complicated, three-dimensional cavities could be a major advantage. Disadvantages embody the requirement to machine the conductor, a lot of complicated conductor wear management problems and occasional difficulties in flushing the cut.
EDM may be utilized in hole-making operations. If atiny low pilot hole is pre-drilled within the work, wire may be rib through, and standard wire EDM used. wherever this is often not possible – in blind hole applications, for instance – a specialised EDM hole creating machine may be used. normally known as a “hole popper,” these machines use a rotating semiconducting tube because the conductor, with endless flow of material (usually deionized water) to flush the cut.
This technology is additionally used with wire EDM machines to make the pilot hole necessary for wire threading. Accurate, precise holes square measure attainable and have allowed for many advanced technologies. maybe the foremost necessary is that the use of EDM created cooling holes in warmth alloy rotary engine blade sections. this allows a “film cooling” method, that permits jet engines to control at higher temperatures for bigger sturdiness and potency.
Why EDM?
In sensible terms, EDM overcomes a significant issue with standard machining: hardness.
In ancient machining processes, metal workpieces square measure usually made up of special grades of hardenable tool steels, that square measure machined in associate degree toughened or soft state to facilitate cutting.
After the specified form is machined, the elements square measure then hardened by one or a lot of heat treatments. This adds time, price and may alter the finished parts’ dimensions, particularly if a poorly controlled heat treatment method is employed. EDM, however, will cut hardened materials and exotic metal alloys and as a bonus produces wonderful surface finishes, ofttimes reducing the requirement for post machining grinding or surface treatment steps.
Like all machining processes, EDM could be a leveling act between speed and surface end. In wire EDM processes for instance, it\'s common to use a quicker, rough-cut followed by the finishing or skimming cut, that uses a less aggressive flushing profile to attenuate wire deflection. Material removal may be exactly controlled, usually measured in “tenths.”
There is plenty a lot of to mention regarding discharge machining. Future articles can dig deeper into this versatile, noncontact cutting technology. Below square measure many example EMD machines.
New generator idea, simple threading wire EDM
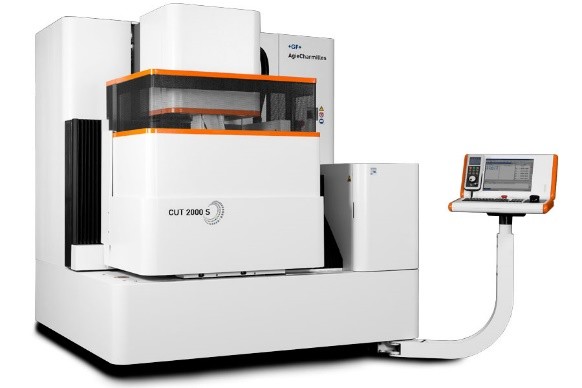
GF AgieCharmilles’ CUT 2000S options a replacement generator idea, a module for simple wire threading beneath troublesome conditions, availableness of in-process measuring and automatic half and power dynamical. The CUT 2000S has been shown to scale back machining time by thirty % and turn out high-quality surface finishes of Ra ≤0.08µm.
Ram EDM with automatic tool dynamical and adaptational controls
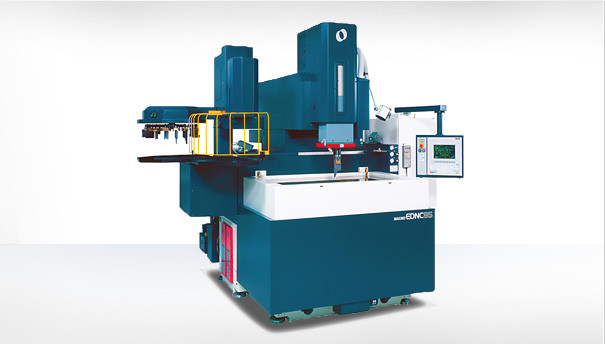
Makino’s EDNC85 Ram EDM machine combines rugged construction, easy programming, and advanced style and performance options for correct EDMing of enormous workpieces. Equipped with a “Rib Head” attachment, this huge machine will turn out deep ribs as quick as or quicker than the tiniest Ram EDM machines on the market. Automatic tool amendment and adaptational controls alter high levels of unattended machining. “A-Jump” – automatic jump machining management – sets jump conditions to the machining job, eliminating the requirement for operator intervention.
Backlash-free bridge style wire EDM
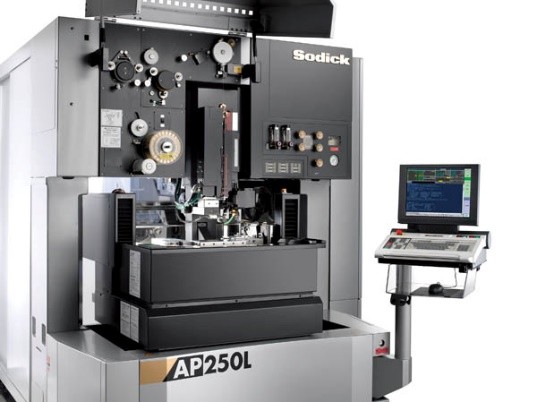
The Sodick AP250L wire EDM machine uses a linear motor drive system, in addition to a bridge style for improved positioning and machining accuracy. It takes advantage of backlash-free precise axis movement, whereas minimizing the deformation of the machine structure. The new developed LN2W power provide unit is featured on the AP250L and utilizes \"Perfect Active Control\" technology and uses one Gbit/sec serial communication technology that includes high-speed process of the discharge management and motion management during a cooccurring method.
Automatic wire threading while not material evacuation
The AU-1440iA Z800 Submerged Wire EDM From Absolute Machine Tools is designed to method tiny in addition as giant elements up to sixteen,400 pound in weight. Automatic wire threading enhances machining speed by accomplishing quick submerged rethreading at the break purpose. once wire breakage happens, rethreading takes place while not material drainage/refilling, leading to spark-to-spark times as low as fifteen seconds. A 64-bit Windows CE-Based computer CNC system drives machine axes via control system, direct coupled AC servomotors, with eight millionths resolution confirmed by a Heidenhain linear glass scale feedback system.
Cylindrical motor eliminates cogging
The Mitsubishi MV-Series EDM machines feature a replacement cylindrical drive motor, sanctionative higher speeds and exactness while not cogging or time prices. The MV Series options a T-shaped base casting with direct axis mounting for improved accuracy, higher rigidity and sander movement. The MV servo control\'s fiber-optic drive system and V350 type-5 generator accelerates latent period and accuracy, and reduces conductor wear and vibration. The MV-Series auto-threader uses fourteen inches of toughened wire length with the redesigned coordinate axis for tall elements and reduced wire curl magnitude relation.
I am glad that I saw this post. It is informative blog for us and we need this type of blog thanks for share this blog, Keep posting such instructional blogs and I am looking forward for your future posts.
ReplyDeleteProgrammable logic controller